After months of planning, designing, and testing, you finally have your prototype ready. But moving straight into full-fledged production may not be the best next step in your process. Although the prototype might be good now, what if there are adjustments that need to be made? Spending money on a full production run may end up costing more in the long-run.
Consider, instead, doing a development test run with RTV silicone molding. There are advantages to running an in-between development test, checking for fit and function, which will help ensure that the final product will be as exact as the prototype.
RTV silicone molding can help bridge the gap between prototype and final production; it provides a more cost-effective way to test out components. Parts created from RTV silicone molding are similar to the prototype, mirroring color, form, and function, but tend to be less expensive to produce in low-volume manufacturing, making it an ideal solution.
RTV Silicone
RTV silicone, or Room Temperature Vulcanized silicone, is a liquid silicone compound that cures at room temperature to create a rubber that is flexible and can capture almost any amount of detail. The silicones are created from mixtures of silicone polymers, fillers, and silane catalysts, while fillers like acetic acid help speed up the curing time of RTV silicones.
They are available as a one-component product or a two-component product. One-component RTV silicones are composed of a one base component and do not need to be mixed with anything before production. Two-component RTV silicones have a base that is then mixed with an activator component. The activator component is typically what helps create a faster setting time.
Depending on which compound is being used, RTV silicone comes in a range of hardness, from very soft to medium, making it useful for a variety of products. The rubber that is produced can be used for molding, as an adhesive sealant, and for everyday crafts. The automotive industry uses RTV silicone to create gaskets in-place. It is also commonly used as a household sealant.
What is RTV Silicone Molding?
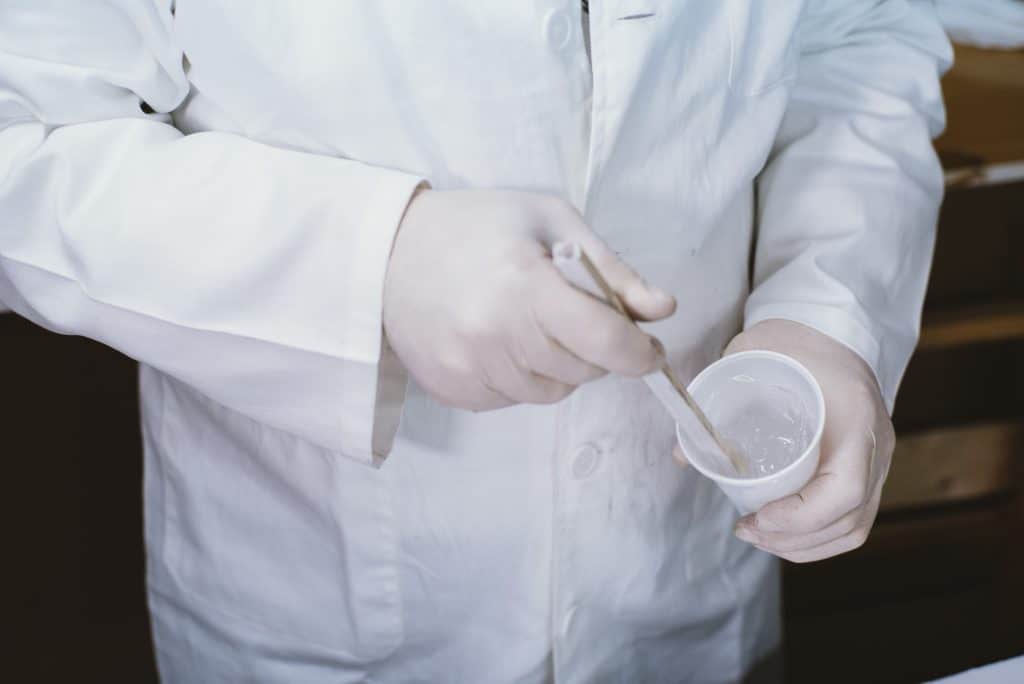
Due to its unique properties, RTV silicone is excellent for mold-making; its flexible nature will fit any mold and be extracted in the mold’s exact shape, complete with intricate details.
To produce a product using RTV silicone molding, a pattern must be first made. This pattern can come from an already created prototype. If the material is suitable, such as wood or metal, the silicon can be applied directly to it, forming the pattern.
Otherwise, a pattern can be formed out of wood, metal, or a 3D printed model. While wood and metal have been the more traditional route, 3D printing patterns allow for a faster lead time and can reduce the overall cost. RTV silicone molding is a type of additive manufacturing that has become more popular over time due to its inexpensiveness and that it doesn’t waste as much material in the process.
Once the pattern has been created, the chosen silicone is mixed with a curing agent, if it’s a two-component silicone, and poured over the pattern. Depending on the mold, the curing time can take up to 24 hours before it is ready. After the mold has set, the product is ready to be used as intended.
RTV silicone molding uses
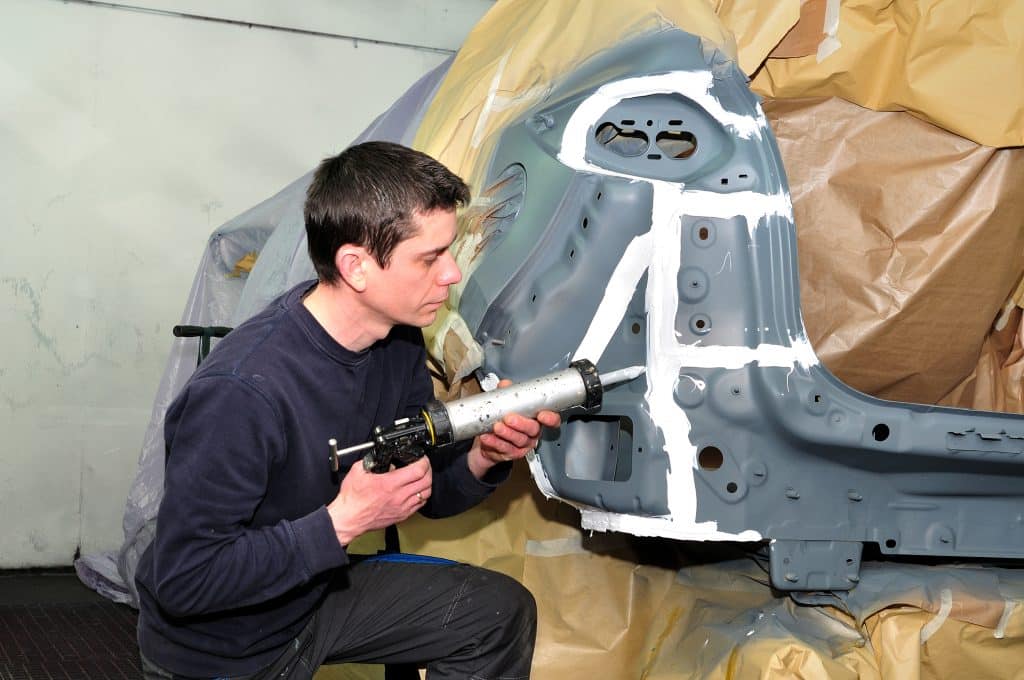
Using RTV silicone molding provides a fast and cost-effective way to create products as well as in-between prototypes for design checks and testing its usability. Unlike other manufacturing processes, RTV silicone molding is meant for low-volume production; typically between 15-30 units per mold, although each mold can usually be used for up to 100 units.
This makes RTV silicone molding an ideal solution for product demonstrations, functional testing, prototyping, and small-production runs of a product. Almost any industry can benefit from RTV silicone molding, but the top users of the manufacturing process are:
- Automotive
- Aerospace
- Medical
- Robotics
- Dental
- Electronics
- Military
- Consumer Products
Types of RTV Silicone Molding
RTV silicone molding rubbers use two different types of silicone chemistry to form an elastomer, often referred to as RTV-2 silicone. The two types of systems are condensation cure systems, which use a tin based catalyst, and addition cure systems, which use a platinum-based catalyst.
Condensation cure systems
Condensation cure systems rely on tin catalyzation. They are excellent for general mold making and prototype applications as they can cure at room temperature over almost any type of surface, with only minimal shrinkage percentage. You can increase the speed of which they dry by mixing in special activators, making them perfect for projects that need to be completed quickly.
RTV Silicone molds that use condensation cure systems can be used for casting masonry, candle wax, polyester, epoxy, polyurethane, and gypsum. Projects that are looking for a cost-effective way to produce prototypes or molds would find condensation cure systems the ideal choice.
Addition cure systems
Addition cure systems are platinum based and tend to be more expensive than condensation cure systems, which rely on tin. They also provide less shrinkage and more heat resistance, allowing them to cure faster when exposed to heat. The downside to addition cure systems is that they can be inhibited by sulfur, tin, or animes.
Products made using the addition cure system have a longer mold life compared to the tin-catalyzation. Those who are looking for more of a permanent product using RTV silicone molding should look to addition cure systems. They are ideal for casting epoxies, polyurethanes, and low-melting point metals.
Other RTV Silicones
A third type of RTV-silicone, RTV-1 silicones, are made from one-component condensation curing materials. RTV-1 silicones are used for caulking or sealing materials and must be exposed to moisture in the air to cure. Unlike RTV-2 silicone, RTV-1 silicones are not meant for fully forming molds or other parts, but can be used to seal or assemble part of the project.
What are the Benefits of Choosing RTV Silicone Molding?
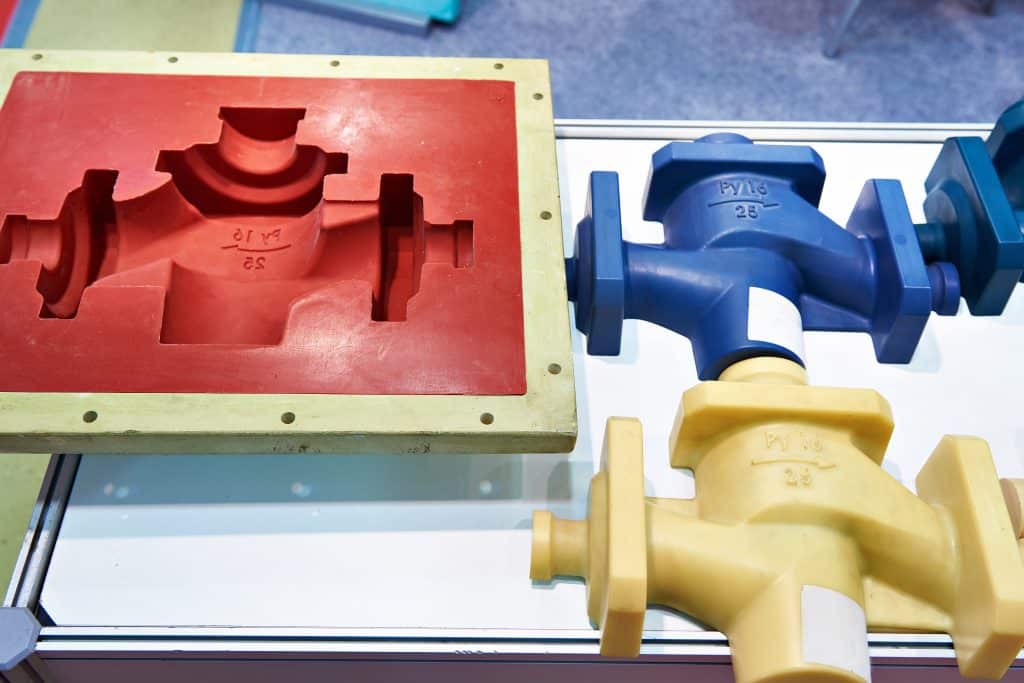
Instead of jumping straight from prototype to full production run, choosing to produce RTV silicone molds of your product has many benefits. In addition, RTV silicone molds can be used for finished products, especially when utilizing the addition cure system.
Exact replicas
RTV silicone molding creates near perfect replicas of the patterns they are formed over, including intricate details and complex geometry that would otherwise be lost in different manufacturing processes.
Creating a perfect product in one process means there are minimal post-production processes, which helps save money and time.
Low-volume manufacturing ready
The process is ideal for those needing a small to medium run of items, as most mold patterns can create up to 100 units. If more are needed, another pattern can be created, often in a short amount of time.
Unlike other low-volume manufacturing processes, such as traditional 3D printing, silicone molding can create larger products and parts complete with details, even at a lower production volume, without affecting the run time.
Faster run time
While the traditional approach to RTV molds used to be machine patterns, which could take one to several weeks, silicone molding is faster with the ability to add curing agents to set up almost any item or part overnight.
The additive manufacturing process reduces the time it takes to create the pattern and mold, as well as cuts down on the price and labor needed. With a faster lead-time, products are able to be tested and re-designed as needed before they are sent to a full-production run.
Cost-effective
Pricing of a product using an RTV silicone mold will vary based on the size and geometry of it, as well as the finishing coating, such as texture and primer. While the initial cost of the project when broken down to an individual part may appear expensive, RTV silicone injection costs much less than other manufacturing processes such as injection molding, with an increased run time as well.
Reduce Risk with RTV Silicone Molding
Due to the fact that RTV silicone molding is cost-effect, has a faster run time, and can create a part or item with intricate, exact details, using it for your next project reduces risk. By utilizing RTV silicone molding, you are able to produce a product from an idea into a prototype that can be tested and redesigned as needed with low initial investment. With a faster run time, any project has flexibility to change and adapt to any customer changes or demand.
Contact Philbrook Corporation to see if the benefits of RTV silicone molding can help you complete your next project.